Exploring Plasma Spray Coating
Introduction
Plasma spray coating utilizes electrically generated plasma to melt and propel materials onto substrates at high velocities for surface engineering. Powder feedstock, often metals, ceramics, or composites, injects into the plasma jet where extreme temperatures rapidly melt the particles into a molten state optimized for coating adhesion. The technique can treat large surface areas with thickness from 20 microns to several millimeters at much faster rates than PVD or CVD methods. Plasma spray coating provides exceptional flexibility, able to deposit virtually any material in a simple single step process ideal for enhancing wear, heat, and corrosion resistance.
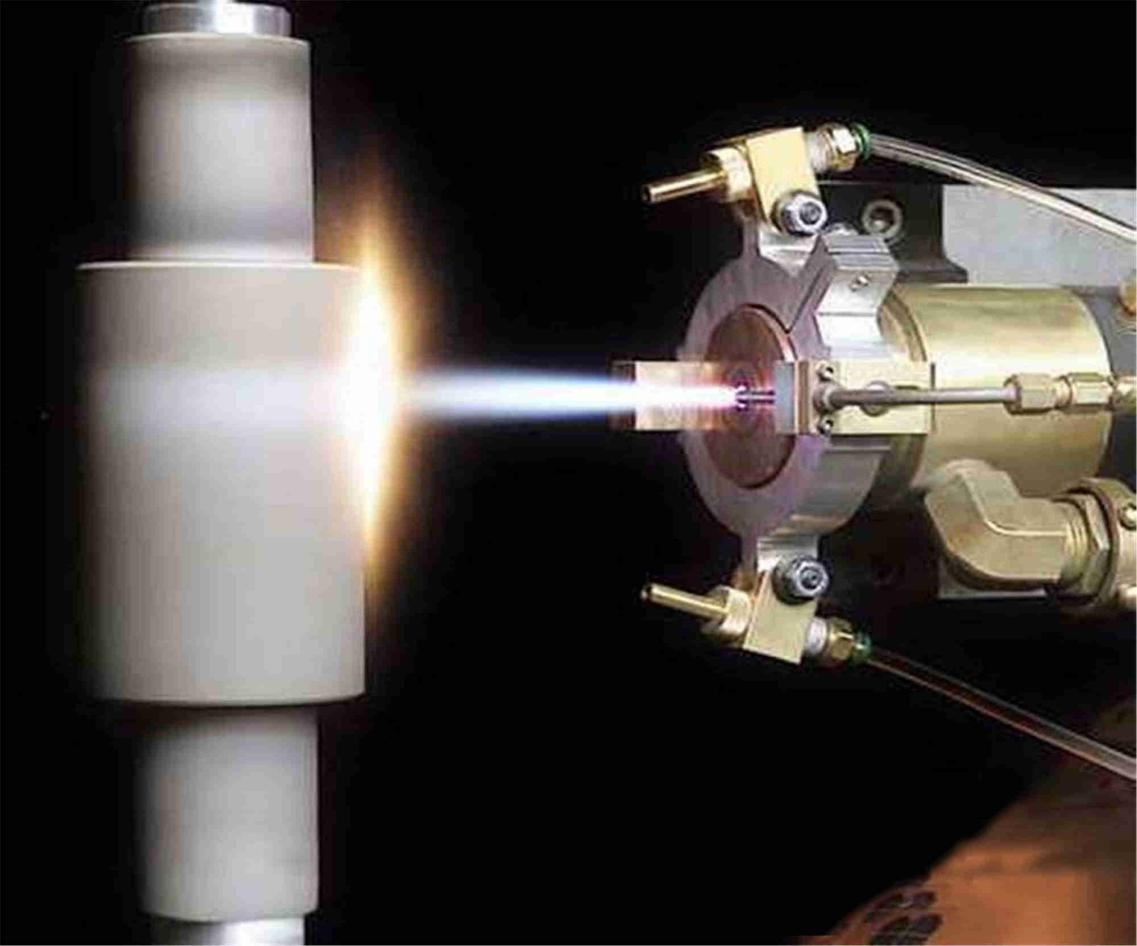
Plasma spraying process
Achieving quality plasma spray coatings requires careful control over the complex interactions between feedstock, plasma jet, and substrate. Powder feedstock injects into the 10,000°K plasma stream where rapid melting transforms particles into uniform droplets. The plasma jet then accelerates the molten material at supersonic velocities towards the substrate surface. Optimizing variables like jet velocity, particle state, and impact angle enables the molten droplets to flatten and solidify, creating a well-bonded coating with the desired characteristics. Precise regulation of every step allows plasma spray to deposit extremely high-performance coatings unmatched by other methods. Unlike sputtering, spray coating usually don't need a vacuum chamber.
Properties
Four key factors define plasma spray coating properties: the coating structure ranging from amorphous to crystalline, porosity levels, adhesion strength to the substrate, and resulting surface roughness. Carefully optimizing these interdependent properties enables tailored coatings for specific applications.
l Coating Structure- Spherical powder particles flatten upon impact, producing laminar splats overlaying the surface. This layered splat structure ranges from amorphous to crystalline depending on powder composition and plasma conditions.
l Porosity- Plasma spray coatings contain pores between splats ranging from <1% to >15%. Finer powders and optimized plasma parameters minimize pores for denser coatings.
l Adhesion Strength- Roughening the substrate surface through grit blasting optimizes mechanical interlocking between coating and substrate. Removing rust or oxidation also enhances adhesion.
l Surface Quality- Coatings up to 0.5mm thick provide protection while minimizing residual stress and potential spallation. Excessive thickness induces high stress leading to poor coating quality.
Carefully controlling these interconnected properties allows engineers to tailor the coating structure, density, bond strength, and surface finish to meet application requirements with optimal plasma spray parameters and powder characteristics.
Advantages
l Versatility - Plasma spray can deposit almost any material that can be melted, including metals, alloys, ceramics, polymers, and composites. This allows a wide range of coatings.
l Adhesion - The high kinetic energy of the plasma jet produces coatings that mechanically bond very well to the substrate. This provides excellent adhesion.
l Dense coatings - Plasma spray can produce very dense, low porosity coatings through optimization of spraying parameters.
l Thick coatings - Coatings ranging from 20 microns up to several millimeters thick can be applied in a single pass. Other techniques are limited in coating thickness.
l High deposition rates - Deposition rates can reach 100-200 microns per minute, much faster than PVD and CVD. This enables high throughput.
l Large areas - Plasma spray can coat very large surface areas efficiently at high deposition rates.
l Low substrate temperatures - Substrate temperatures remain low, avoiding damage or change to substrate properties.
l Surface properties - Coatings can provide enhanced hardness, wear resistance, corrosion resistance, thermal insulation, etc.
l Single-stage process - No pre-treatment or post-treatment steps are required, simplifying the coating process.
Disadvantages
l Porosity - There is often some porosity in plasma spray coatings, which can allow corrosive substances to reach the substrate. Proper optimization is needed.
l Surface roughness - The layered splat structure results in a rougher surface than PVD or CVD coatings. Post-treatment may be required.
l Line of sight - Complex geometries with recesses or blind holes are difficult to coat evenly. Robotics or manipulation of the part is needed.
l Thermal properties - Thermal conductivity is lower than bulk materials due to lamellar structure and defects between splats.
l Residual stresses - High quenching rates can induce residual stresses leading to poor coating adhesion. Stress relieving post-treatments may be needed.
l Equipment cost - Plasma spray systems require significant capital investment and large facilities. This can limit applications.
l Limited materials - Some materials, like organics and pharmaceuticals, are difficult to plasma spray due to decomposition.
l Operator skill - Achieving high quality coatings requires an experienced operator and strict process control.
l Part size - The coating chamber limits the maximum part size. Very large parts require custom systems.
Applications of Plasma Spray Coating
Aerospace- Thermal barrier coatings, wear coatings, thermal management, corrosion protection for aircraft and rocket engines.
Power generation- Thermal barrier coatings for gas turbines. Corrosion and wear resistance for turbine blades, boilers, and other components.
Automotive- Cylinder liners, camshaft coatings, brake discs, suspension components to improve wear, friction, and heat resistance.
Biomedical- Hydroxyapatite coatings on prosthetics and implants to enhance biocompatibility and osseointegration.
Printing- Wear resistant coatings on rollers and print heads. Corrosion protection for ink tanks and pipes.
Textile- Anti-stick coatings on presses, rollers, irons and cutters. Corrosion protection on drier cans and pipes.
Petrochemical- Anti-corrosion coatings on tanks, pipes, valves, pumps. Wear coatings on impellers, agitators.
Defense- Corrosion resistance, thermal management, radar absorption and ballistics protection for vehicles, aircraft, vessels.
Cutting tools- Wear resistant coatings on drills, saws, milling cutters, punching and forming tools.
Conclusion
With durability and versatility, plasma spray coating serves industries globally as a premiere thermal spray method that mechanically bonds robust, functional coatings onto surfaces for enhanced performance.