Comparing Electron Beam Evaporation and Thermal Evaporation
Electron beam evaporation and thermal evaporation employ physical vapor deposition to coat substrates, yet each process boasts distinct mechanisms and capabilities. Comparing the evaporative sources, deposition kinetics, and coating attributes elucidates the advantages and limitations, empowering informed selection between these ubiquitous PVD techniques.
|
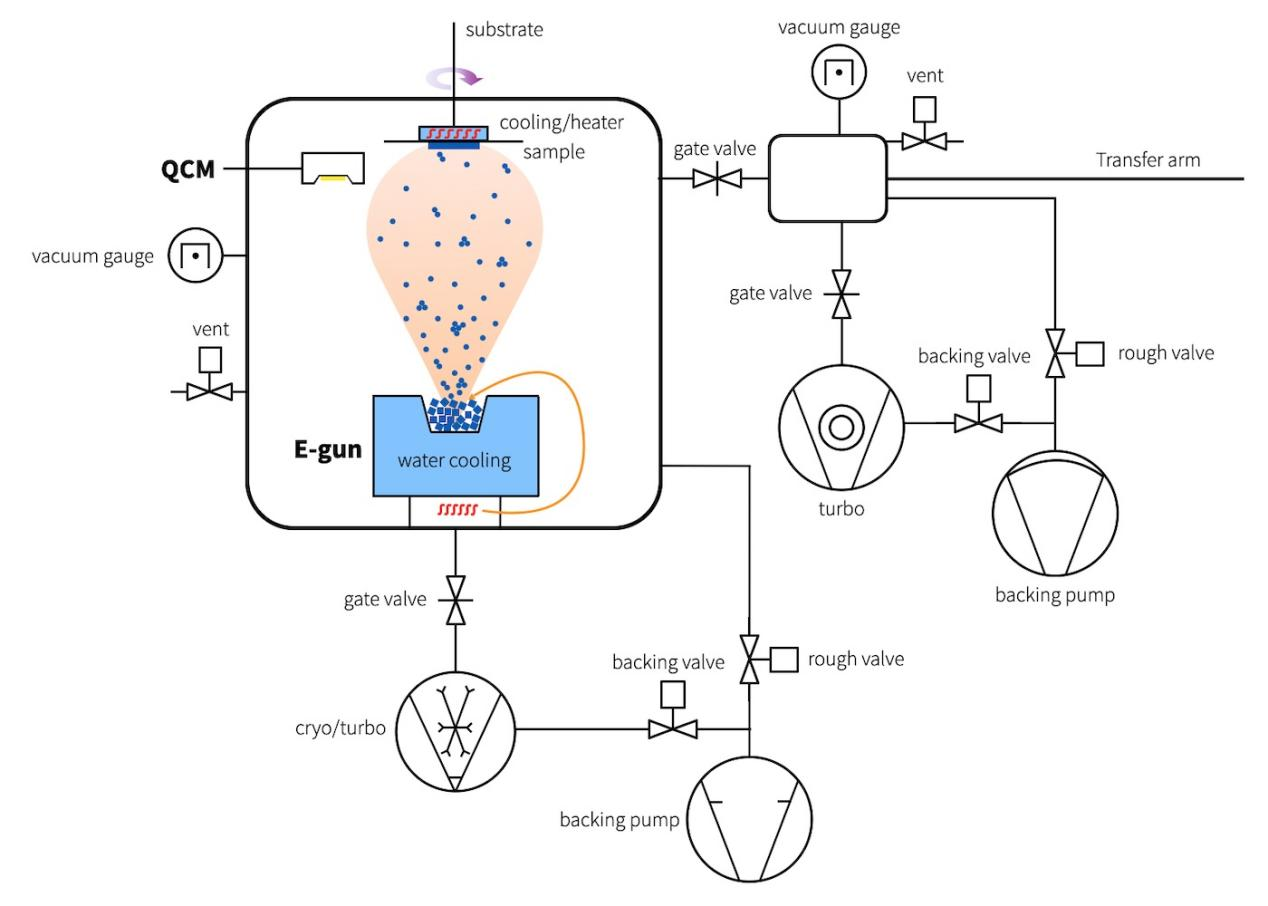
Physical Vapor Deposition
As a vacuum deposition technique, physical vapor deposition (PVD) enables durable, corrosion-resistant coatings on substrates like ceramics, metals, and glass under low pressure environments. Unlike other thin film techniques, PVD's vaporized sources and controlled condensation kinetics minimize ecological impacts. Cutting tools, decorations, and anisotropic gases exemplify applications benefitting from PVD's dense, uniform films. The environmentally-friendly nature and outstanding coating properties make PVD a premier choice for producing enhanced surface films across industries.
What is Electron Beam Evaporation?
Electron beam evaporation utilizes high-energy electron bombardment to induce physical vapor deposition onto chamber contents. An accelerating electric field focuses electrons from a negatively charged tungsten filament into the positively charged anode target. Atoms ejected from the vaporized target transition to the gas phase before depositing line-of-sight coatings within the vacuum chamber. Precise control over electron energies and beam focusing enables uniform evaporation critical for high-quality PVD films.
Advantages
With extremely high heating capacity, electron beam evaporation rapidly vaporizes materials like refractory metals at higher rates than thermal methods. The intense energy density provides precise control over the deposition, enabling very pure, dense films. However, electron beam deposition produces thinner coatings than thermal techniques. The exceptional vaporization temperatures, deposition speed, and superior film quality make electron beam evaporation ideal for specialized applications requiring pure dense coatings.
Disadvantages
Line-of-sight deposition limits electron beam evaporation's ability to coat complex geometries fully. Moreover, filament degradation can decrease deposition uniformity over time. Ultimately, the high capital and maintenance costs make electron beam evaporation more expensive than comparable PVD processes.
Thermal Evaporation
In thermal evaporation physical vapor deposition, heat evaporates materials like elemental metals or compound molecules for deposition onto substrates including semiconductors, solar cells, and optical components. Its versatility in depositing various materials onto diverse substrates makes thermal evaporation a prevalent PVD technique.
Thermal evaporation coats substrates by heating source materials to vaporization inside a vacuum chamber. As the solid material vaporizes, the resulting gas phase condenses onto chamber contents, depositing a thin film coating. This vaporization and deposition mechanism enables thermal evaporation to adhere uniform coatings onto substrates under vacuum conditions.
Advantages
l Applicable to a wide array of materials, both metals and nonmetals, especially low melting point alloys like those with mercury
l Simple methodology, equipment, and operation makes thermal evaporation easily implemented and understood
l Low equipment costs and maintenance requirements provide a very affordable physical vapor deposition technique
l Ideal for cost-conscious applications with low melting point deposition materials that benefit from uniform vacuum coatings
Disadvantages
l Lower purity films compared to electron beam evaporation
l Relatively low density coatings
Similaritiesand Differences
Electron beam evaporation and thermal evaporation both utilize physical vapor deposition, where source materials vaporize to deposit coatings on substrates. The vaporization, transportation in a vacuum, and condensation mechanisms define these two evaporation-based PVD processes, underlying their commonalities despite distinct heating methods.
While both utilize vaporized precursors, electron beam and thermal evaporation differ significantly in their vaporization mechanisms, as evident from their names. Electron beam bombardment supplies intense energy to directly decompose source materials, whereas thermal evaporation relies on heating crucibles via electric resistance to melt and vaporize contents. The crucible-less electron beam process maintains purity by avoiding contact with container walls. In contrast, impurities can contaminate thermal evaporation films from dissolution of the crucible into the molten source material. However, using dedicated crucibles for individual materials can mitigate contamination. Ultimately, electron beam evaporation’s crucible-free operation enables exceptionally pure coatings unmatched by thermal evaporation. But for some cost-sensitive applications, thermal evaporation can provide adequate quality at lower equipment expense by proper crucible selection.
Applications
Solar Cells
With deposition versatility, both electron beam and thermal evaporation prove vital for coating thin-film solar cells with materials like silicon, indium, CIGS, and more. Their precision control over film thickness and composition enables high-efficiency photovoltaic devices.
OLEDS
Employed in OLED manufacturing, electron beam and thermal evaporation precisely deposit organic thin films crucial for high-performance devices.
Optical Coating
With unparalleled coating abilities, electron beam and thermal evaporation prove invaluable for depositing precision thin films onto optical components like lenses and mirrors to either reduce or enhance reflections as desired. Their vapor deposition techniques enable exquisite control over optical thin film properties, making these PVD processes essential for specialized optical coatings.
Conclusion
Selecting between electron beam and thermal evaporation demands evaluating key factors like cost, durability, purity, yield, and quality. The ideal technique provides the optimal combination of performance, production, and economics for an application's specific coating requirements. Thoughtfully weighing these considerations ensures proper physical vapor deposition method selection.